Offline Selective Wave Soldering Machine
- max solder temperature 350℃
- solder pot capacity 15 KG
- dimension L1280mm X W1400mm X H1650mm
- Net weight 380KG
- Product description: Offline Selective Wave Soldering Machine max solder temperature 350℃ solder pot capacity 15 KG dimension L1280mm X W1400mm X H1650mm Net weight 380KG
-
INQUIRY
Offline Selective Wave Soldering Machine
Products description

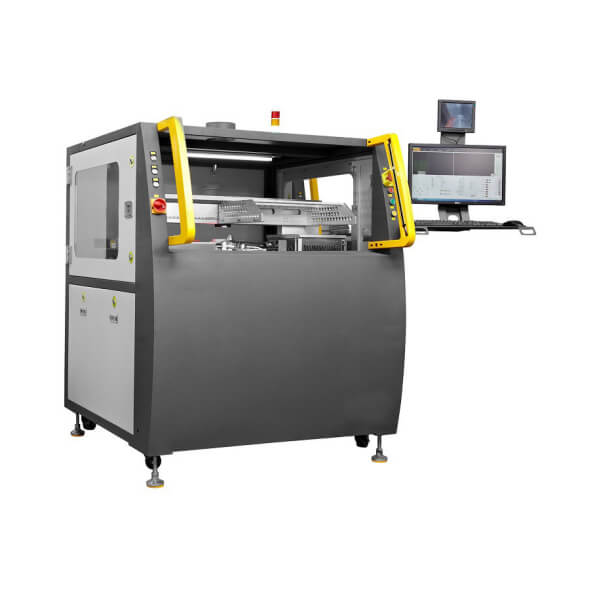
Offline Selective wave soldering machine is on economic solutions for the selective soldering process, Cheap price:30000USD and you can got an idea machine dealing with the small quantity selective soldering PCB. The producing speed around 1minites/PCB.
selective wave soldering machine with automatic system and easy wave soldering process for led outdoor display
we not only have the standard wave soldering machine, but also have the selective wave solder machine which include online and offline!
Introduce:
1.More and more competition in the electronics market, to the electronic product manufacturing enterprises bring huge quality and cost pressures.Electronic products production process of high density, miniaturization trend driving the rapid development of SMT technology, the traditional wave soldering process have been unable to meet the needs of the few remaining perforation components of welding, and manual mode is difficult to for large heat capacity or fine pitch components to realize high quality, high efficiency welding, the machinery, equipment and labor cost advantage is gradually lost.Mini selective wave soldering technology to the development of electronic product manufacturing engineers provide a new choice, at the same time, choose welding low running cost and high applicability to quickly get the welcome of electronic products manufacturers.
2.Selective wave soldering system is a kind of controlled by the program, the installation will help flux nozzle and tin furnace of multi-axis control platform.PCB online via rail transportation after positioning, will first spray flux accurately on the PCB for welding on site, and then through a small nozzle (usually 2 ~ 4 mm) in diameter and solder pump to create an accurate circular mini solder wave, after multi-axis control platform, from the bottom of the PCB welding.Due to welding components usually surrounded by SMT components, and high density, small spacing, in order to avoid damage to the bottom of the adjacent components and welding plate, selecting welding process must be very precise.
3.Selective wave soldering system of process control, no matter from movement, process speed, or unlimited direction control (X, Y, Z), temperature and heat control, its function is very powerful.Selective wave soldering during welding, welding parameters of each solder joint can be "tailored", enough process adjustment space to each spot welding conditions (such as: flux spraying quantity, welding time, welding height, wave height) transferred to the best, the defect rate reduce.All the control parameters settings can be saved to the program, at any time during production, can bring up the related data from the program.Therefore, if the system is properly maintained, a few years later, the quality of welding is still the same.
Machine breakdown show
Composition of1:Machine software system
A.With completely independent intellectual property rights of choosing welding software, combined with years of choosing welding using technology, based on the development of the WINDOWS software function, humanized operation with good traceability.
B.PCB pictures or GERBER file can be directly used for the path programming, the path to the starting point, the welding speed, idle motion speed, height of Z axis, such as wave height can be set on the computer.Domestic equipment industry the only can import the two formats of programming software.
C. after compiling the path of a piece of plate, can through the array function to path of makeup, at the same time on the choice of welding fixture some location of PCB.
D.the real-time display of welding process.Through the camera to the computer software, can take photo of the welding process, video recording and preservation.
E.the database function.Customers to use software increases with time, and constantly add solder and flux, the kinds of record is generated for each product, the more perfect.Record to welding different kinds products using flux, solder type, welding parameters, product parameters, etc.
F.Key parameters of the software completely monitoring, such as temperature, speed, air pressure, the nitrogen pressure and so on.
G.It can be upgraded to automatic wave height correction function.How many pieces of plate can be set interval correction wave height at a time.
H.It can be upgraded to take MARK point positioning and the frequency of use.
Composition of2:Motion platform system
A.motion platform design whole aluminum casting, lightweight design, and to improve the running speed of the platform rigidity.
B.Panasonic servo driver provided with Panasonic motor sports motivation, silver ball screw and linear guide for direction, positioning precision, low noise, smooth movement.
the mobile platform with dust-proof plate, prevent dirt drip into the ball screw.
Composition of 3:Spray part
A.the nozzle adopt Japanese origin atomization nozzle, atomization effect is good, and not easy blockage, suitable for various types of flux.Can be upgraded to choose German origin of jet nozzle, applies only to solid content less than 5% of flux.
B.flux filling and storage is adopted, and guarantee the spray pressure constant, the influence of flux is not helped by how much.Air pressure through the electronic gauge feedback to the computer monitor, in order to ensure the effect of the spray.
Composition of 4:Preheating part
A.All top and bottom with shoots the far infrared heating, the position is adjustable.
B.the heating rate can adjust the computer.
Composition of 5:Selective tin stove part
A.tin stove temperature, nitrogen gas temperature, wave height, wave correction, etc. Can be set in a computer
B.tin furnace tank for titanium alloy is made, no leakage.External type heating plate, uniform heat transfer.
C.tin stove adopts quick connector wire, tin stove replacement without rewiring.
D.nitrogen on-line heating devices, and ensure good wettability and reduce oxide tin stove.
F.tin stove with tin stove liquid level alarm.
G.the nitrogen pressure in through the electronic gauge feedback to the computer monitor, in order to ensure the effect of nitrogen protection.
Composition of 6:Transmission mechanism
A.spray and preheating section rail use chain transportation, guide rail, respectively before and after using independent stepper motor drives, transportation speed can be set.
B.tin stove on the stainless steel roller, guide adopts independent stepper motor drive, respectively before and after running smoothly, use for a long time without any abrasion.At the same time guarantee the tin furnace nozzle can achieve the most edge 3 mm PCB.
C.transport guide with splint, ensure accurate positioning.
Composition of 7:The machine shell
A.At the bottom of the whole steel structure, and substrate to increase the stability of the machine, reduce the vibration.
B.Machine industrial paint surface.
machine parameters
Machine name
|
Flason-450
|
General Function:
|
dimension
|
L1280mm X W1400mm X H1650mm
|
general power
|
5kw
|
consumption power
|
1--3kw
|
power supply
|
1 PH 220V 50HZ
|
net weight
|
380KG
|
reuiqred air source
|
3-5 Bars
|
required air flow
|
8-12L/min
|
required N2 pressure
|
3-4 Bars
|
required N2 flow
|
≥2m³/Hour
|
required N2 purity
|
≥99.998%
|
required exhausting
|
500--800CMB/H
|
carrier or PCB
|
carrier
|
Customized
|
max carrier size
|
L450 X W300MM
|
max solder area
|
L400 X W300MM
|
PCB thickness
|
0.2mm-----6mm
|
pcb edge
|
3mm above
|
controlling & conveyor
|
Controlling System
|
Industrial PC
|
PCB Loading board method
|
Manual
|
PCB Unloading board method
|
Manual
|
Operating height
|
900+/-30mm
|
PCB conveyor up clearance
|
50MM
|
PCB conveyor bottom clearance
|
30MM
|
Motion table
|
|
motion axis
|
X, Y, Z
|
motion control
|
Servo control
|
position accuracy
|
+ / - 0.1 mm
|
chassis
|
Steel Constructure
|
Flux management
|
flux nozzle
|
jet valve
|
flux tank capacity
|
1L
|
flux tank
|
|
Preheat
|
preheating method
|
Bottom Infrared preheating
|
heater’s power
|
3kw
|
temperature range
|
25--240c degree
|
solder pot
|
standard pot number
|
1
|
solder pot capacity
|
15 kgs /oven
|
solder temperature range
|
PID
|
melting time
|
20--30 Minutes
|
max solder temperature
|
350℃
|
solder heater
|
1.2kw
|
solder nozzle
|
nozzle dim
|
Customized
|
Nozzle material
|
Steel alloy
|
standard equipped nozzle
|
5pcs/oven(inner 4mm x 3pcs,5mm,6mm )
|
N2 management
|
N2 heater
|
Standard
|
N2 temp range
|
0 - 350 C
|
N2 consumption
|
1---2m³/hour/nozzle
|
1.Short lead
PREVIOUS:SMT Stencil CLEANING MACHINE 5600NEXT:Full Automatic Online SMT solder paste Stencil printer GD450+
RELATED PRODUCTS
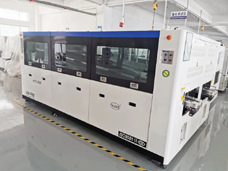
Dual Rail Wave Soldering machine
Dual Rail Wave Soldering Machine KTU-350D Manufacturer, Preh...

Wave Soldering Machine
China Wave Soldering Machine KTU-350 Manufacturer, Preheatin...

Mini wave soldering machine
Mini wave soldering machine, Weight: 700KG, Dimensions: 2100...

Small wave soldering machine
Small wave soldering machine, Weight: 700KG, Dimensions: 260...
CATEGORIES
LATEST NEWS
CONTACT US
Contact: Mr Tommy
Phone: +86 13691605420
Tel: 0755-85225569
Email: sales@flason-smt.com
Add: No.94,Guangtian Road,Songgang Street,Bao an District